Using Simulators for Training Individuals to Efficiently and Safely Operate Logging Equipment
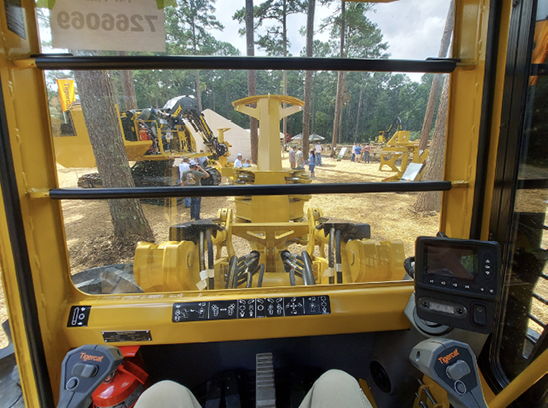
A simulator can be defined as a machine or process with a set of controls similarly designed to produce a realistic imitation of the operation of a vehicle, train, boat, aircraft, or other complex system and used for training purposes. There are many simulators, including flight, racecar driving, and truck driving. There are also simulators that use mathematical approaches to predict forest growth and yield, dynamics of fish and wildlife populations, dynamics of ecosystems, and some of these simulators provide visual depiction of simulation results.
These tools are valuable because they allow individuals to learn about a system or how to operate a machine without actually risking death or bodily harm and without damaging actual structures or machines. Other advantages are discussed throughout this publication.
The logging industry is an extremely important component of the wood supply chain. Loggers harvest and transport raw woody resources from a forest to a processing facility, often called a mill. As with most professions, there are many intricacies that loggers need to be knowledgeable about to best accomplish their job. Additionally, it can be a highly dangerous profession.
Thus, many logging simulators have been developed to help inform and train individuals about the profession. These simulators can range from very basic to highly sophisticated. Some simulators are video games designed more for entertainment, while other simulators are designed specifically for training professionals. However, even the video-game simulators can be used to help educate people about the logging industry, particularly younger people who have limited interest in the logging profession. This publication will mainly focus on more professional-focused simulators, but we will also describe video-game-based simulators.
Utility of Simulators for the Logging Profession
Logging is a very expensive and highly competitive industry; some parts of the country are more expensive and competitive than others. Here, in the Southeast, most logging operations are fully mechanized—no “boots on the ground”—which means there is very little time when logging crew members are conducting operations outside of protected equipment. These fully mechanized operations are highly efficient and productive relative to those from the past, but this efficiency and productivity come at a financial cost.
Most often, logging operations in this region include a feller-buncher (either wheeled, sometimes called drive-to-tree, or less often tracked) and skidders to haul the logs from the stump following the felling of trees to a central processing location, often called a landing. At the landing, there is some process to remove branches and limbs and to merchandize stems. Equipment can include some combination of pull-through delimbers, ground saws, delimbing gates, delimbinators, or tracked processors. A tracked processor is one piece of machinery that can accomplish all the processing tasks that are required using several of the other pieces of processing equipment.
After processing, logs must be loaded onto trucks using a loader, and then the unmanufactured, raw woody resource is transferred by the truck to a mill. In the Southeast, loggers can easily have as much as $750,000 to $1 million invested in their equipment for each separate logging crew. Some logging businesses maintain only one “crew,” but larger businesses can have five crews or more. Increasing loan interest rates put extra pressure on logging operations; carrying “notes” on this equipment becomes extremely costly. Therefore, it is vital that crew members operating this equipment are highly skilled, efficient individuals to help maximize narrow profit margins.
Insurance rates continue to rise, particularly truck insurance, and fuel is becoming increasingly expensive. Plus, as inflation increases, equipment costs rise, the costs of mechanics increase, and the cost of parts increase. The costs of labor also increase as inflation increases, as well as the costs of any fringe benefits supplied to employees. Furthermore, tight quotas from mills and expanding regulations create issues for logging operations. Again, highly skilled, efficient crew members are needed to operate this equipment to help minimize costs and maximize profits as much as possible.
Currently, the majority of machine operators in the logging industry are older than 55 (Conrad et al. 2018) and are nearing retirement age. So it is imperative that younger people become interested in this industry, and it is vital that they have the skills needed to operate this equipment safely and efficiently. Thus, training is an essential need. Simulators are effective tools because they can help provide much of the training without substantial cost and damage to actual machines or injury to trainees and instructors/trainers.
Today, many of the modern machines are operated using skills that are required to play video games (Figure 1). Machines like feller bunchers, skidders, loaders, processors, harvesters, and forwarders require the same skills that many of our younger people obtain by playing video games. Additionally, much of the machinery is automated, thus skills learned from cell phones and computers are very important. In many ways, outside of maintenance and repairing modern logging machines, this equipment is really geared towards our younger generations. So simulators can be wonderful tools to help our younger generation have a “step-up” before actually operating real machines on the ground.
Simulators allow for training of new and experienced operators. Basic skills can be learned from a step-by-step simulator guidance, allowing individuals to become familiar with machine controls. There is also real-time feedback as to how effectively operators are responding to emergencies and mistakes that are made. These machines allow for the tracking of the performance of individuals, providing a means to assess the progression of increasing skill level. Also, the level of productivity of a trainee can be tracked to determine the operator efficiency and, for example, unit costs of logging (machine rate/productivity) associated with that person.
This information can help employers screen potential employees, and perhaps allow employers to assign tasks to individuals who bring increased efficiency to the entire harvesting operation. Individuals can be trained without tying up actual pieces of equipment that are needed by others to actually conduct harvesting operations in the real world. Simulated training can be organized for a whole group of trainees at the same time. Experienced operators of logging equipment can be trained about different or newer equipment by having hands-on training using a simulator of the different or new piece of equipment, thereby reducing start-up costs.
Not only do trainees gain basic skills with a piece of equipment, but they can also learn about adjustments that can be made on the actual machine while training on the simulator. Simulators are also advantageous because swapping of simulated logging machines can be done within minutes, allowing for trainees to be trained on a variety of machines in a short amount of time.
These simulators not only provide training in terms of efficiently and proficiently operating equipment, but they can also be used to train individuals on logger-select thinning harvests and merchandizing and sorting of logs at landings to maximize yields and financial returns. They can perhaps train crew members how to identify tree species while operating the machine, as well as how to select among species to best meet the timber sale objectives. Being able to operate the equipment in a safe and efficient manner is extremely important for reducing costs, but the ability to best merchandize logs and to optimize financial and biological concerns is essential to maximize productivity and profits.
It is important for loaders to know how to position logs on the trucks to maximize payloads in a legal and safe manner. Individuals operating the feller buncher can be trained about many issues related to felling trees, such as logger-select operations. The operator of the feller buncher could be trained about various types of forest conditions that may require different decision-making skills when determining what trees are best to remove. Skidder operators must be able to understand the ergonomics, hydraulic pressures, and mechanical forces of various sizes and number of logs when skidding logs to a landing. Weather conditions can also be changed in many simulators. Operators can even be trained on issues such as best management practices (BMP) or streamside management zones (SMZ). Additionally, these simulators can be used with various languages, such as English or Spanish, and productivity can be measured in English or metric units.
Simulators can also provide initial information about the feasibility of new harvesting techniques or equipment. Experimentation can be done within various forest types and site conditions since most simulators allow users to select the forest type and site conditions. Perhaps harvesting techniques or operations that are conducted very efficiently in monospecific plantations could also be beneficial in mixed-species stands; a simulator could provide some initial feedback.
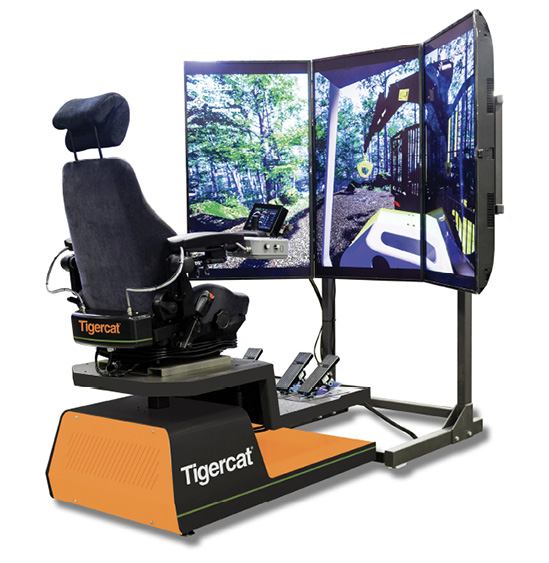

Types of Simulators for the Logging Profession
The majority of the large forestry/logging machine manufacturing companies have simulators available for training. The companies themselves provide information to third-party computer-programming companies about common forest conditions; machine ergonomics, hydraulic pressures, and mechanical forces; and machine size, length, and weight that allow computer programmers to produce accurate visual graphics and for the simulated machines to realistically respond to various conditions encountered by loggers. Some logging equipment manufacturers have different levels of simulators that allow for a more realistic training experience. However, more realism comes at a price. Currently, individual professional simulators can range from $500 to $40,000 per unit.
There are also several video-game simulators. Many of the video-game simulators are $50 or less (as opposed to $40,000 for the more sophisticated professional simulators), and there are many freely available modifications (termed mods) produced by players that can be downloaded by other players.
These video-game simulators may not be as sophisticated as the professional simulators, but they are actually useful because they can help the younger generation learn more about logging and become interested in the profession. Sometimes, even grownups play these games. One product, “Farming Simulator” (FS), is a fairly sophisticated video game that offers a wide variety of equipment choices and tree species to harvest. Two common versions that are commercially available are FS19 and FS22 (GIANTS software). The ergonomics, hydraulic pressures, and mechanical forces associated with operating the machinery are actually quite realistic. There is also the opportunity to buy various pieces of physical hardware (steering wheels, various types of joysticks) to enhance the experience of the simulator. Great advantages of these simulators is the much-reduced cost and the ease of obtaining the game. Users can download from the Internet a licensed version.
One logging equipment manufacturer, for example, offers four different levels of professional simulators: Full, Multi, Compact, and Basic. The Full simulator offers a very realistic experience of someone sitting within the machine and having the same level of controls as the actual machines (Figure 5). For instance, control levers, pedals, and the simulator itself move ergonomically as the actual machine moves in the field. This simulator comes equipped with three large screens synchronized to the simulator itself that allow for a very wide and real-like field of vision. The Basic simulator, on the other hand, is intended to be used with a desktop computer. It has less sophisticated joysticks and no pedals to operate the machine. The joysticks are mounted on the desk.
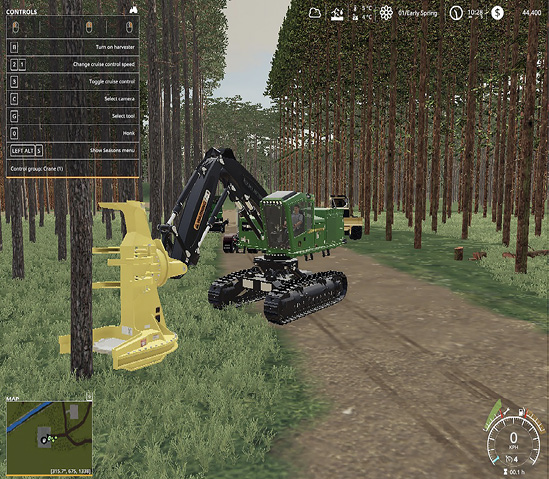
Figure 5. The simulator in the top photo is a logging equipment manufacturer’s Full simulator, and the simulator on the bottom is its Basic simulator.
Hinds Community College Logging Equipment Operator Academy
As part of the Hinds County Community College Logging Equipment Operator program, a full-sized simulator is used to provide trainees an opportunity to operate simulated harvesting equipment before operating actual equipment in the field. This 16-week program is offered twice a year and includes time spent operating the simulator and various pieces of actual equipment in the field. Trainees receive instruction from an instructor, as well as training by others on a variety of topics including BMPs, small-engine mechanics, OSHA training, and aspects of forestry. Students attend the training program 8 hours a day throughout the course, and successful completion of the program leads to several safety certifications as well as Professional Logging Manager (PLM) status. After completion of the course, trainees have sufficient knowledge to be part of an actual logging operation crew. The program is a partnership with the Mississippi Loggers Association (MLA) and the Mississippi Forestry Commission (MFC).
As part of the simulation, a variety of machines can be selected, depending on the training objective of the instructor. Users can select to operate a four-wheeled feller buncher (843L-II), tracked feller buncher (953M/959M), or a skidder (848L-II), all of which are common machines in Mississippi tree-length harvesting operations. These operations are commonly referred to as fully mechanized conventional harvesting systems. By far, tree-length harvesting is the most common logging operation in Mississippi and the Southeast.
Four-wheeled feller bunchers are more common than tracked; however, tracked machines are operated in this region and are advantageous in certain conditions, most notably areas of high slope and extremely wet soils. Some people may refer to feller bunchers as cutters or shears. However, “shear” is not the best term for feller bunchers with cutting heads consisting of disc saws, because they can be confused with actual shear cutting heads still found on some feller bunchers but were more popular in the past.
Additionally, users can select to operate one of two wheeled harvesters (1170G 8W or 1270E), both with a H414 harvesting head, and a forwarder (1510E). The 1170G 8W has eight wheels, while the 1270E has the more standard six wheels. These two machines are commonly used in cut-to-length (CTL) harvesting operations. Although they are less common in the Southeast, CTL operations do exist in this region.
The program at Hinds is unique because it has the only wheeled feller buncher simulator in the country. Based on years of experience running equipment as part of actual logging operations, the second author of this article, who is the instructor at Hinds, believes the wheeled feller buncher simulator operates very closely to an actual machine. The simulator is well designed, mimicking in many ways actual field conditions. Users can select different tracts of timber, allowing them to learn how to operate equipment in a variety of forested conditions. Operators have the opportunity to fell pine plantation pulpwood as part of a thinning operation and to conduct pine and hardwood clearcuts felling sawlog size material. If the instructor chooses, both types of harvests can be simulated on hilly terrain.
As part of the training program at Hinds, experience on the simulator can be paired with operating actual equipment at a site owned and maintained by the MFC near Raymond, Mississippi. Currently, the program does not have an actual feller buncher, but John Deere 648L-II and 848L-II grapple skidders have been used, and students can operate a John Deere 437B loader that can be used to load one of two four-bolster trailers produced by Fryfogle Manufacturing Inc. (FMI) located in Lucedale, Mississippi. This program is operated in large part by the MLA, and several organizations donate time or equipment to help train individuals to operate logging machines, to increase the knowledge of foresters, and to educate the general public about logging operations.
In a workshop setting, several foresters have run the simulator and the actual equipment at the field site near Raymond, providing them an opportunity to learn more about logging operations and identify potential concerns and limitations when operating this equipment. For a variety of reasons, this gain in knowledge is extremely beneficial. For example, they are able to better establish timber sales that meet landowner objectives while allowing for efficient operations by the logger. More efficient operations by the logger have the potential to generate more revenue for the logging firm, the forester representing the interests of the landowner, and the landowner.
Within the simulator, a trainee can fell several rows of timber using the feller buncher and then move over to the skidder and extract felled trees to a landing for further processing. A skilled operator on the wheeled feller buncher can hold (bunch) as many as eight trees in the cutting head before dropping, and then releasing, the current bunch onto the ground, allowing them to go fell and bunch another group of trees. Alternatively, a user can fell trees using a harvester, cut them to desired product length at the stump, and then “forward” them to a landing using the forwarder to be loaded onto a logging truck, hence the term CTL.
There are many helpful minor additions in the simulation world to help operators identify actions in the field that are not desired. For instance, during felling or skidding, if an operator “skins” trees a red ring will appear on the damaged trees, helping the user to identify the damage and to learn how to minimize or eliminate actions that cause that type of damage. Later, the operator can return to the row and remove these “skinned” or “bumped” trees. If an operator lowers the cutting head on the feller buncher too far into the ground, it will “stick” the feller and won’t allow movement of the machine. Users can also erroneously drop felled trees over the top of the feller, teaching operators to use more precision during felling operations to ensure safe control of the tree. Students must pay close attention to detail because the simulator is very unforgiving and does not allow them to make mistakes without notification.
Because this machine is a simulator, there are some slight issues with it. Our second author, the Hinds instructor, has noticed some issues with steering, so the simulated machines are not as maneuverable as the actual wheeled feller buncher or skidder. Additionally, when operating an actual machine, a user has more complete vision of their surroundings than when operating the simulated machines within the simulated forest. There is research into providing head sets and eye coverings to allow for a more complete visualization of the simulated forest from any point or perspective within the simulated forest.
Figure 6. Trainees can pair operation on the simulator with running actual equipment at the Hinds County Community College Logging Equipment Operator Program field site owned by the Mississippi Forestry Commission. Shown in the upper picture is a John Deere 848L-II grapple skidder, while the lower picture contains a John Deere 337E loader (with a pull-through delimber) and two Fryfogle Manufacturing Inc. four-bolster logging trailers.
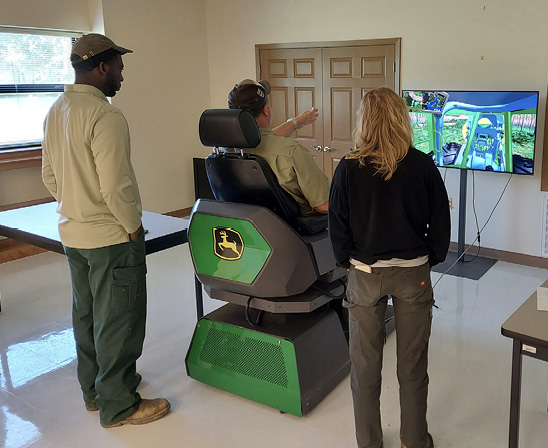
References
J. L. Conrad IV, W. D. Greene, and P. Hiesl. 2018. A review of changes in U.S. logging businesses 1980s–present. Journal of Forestry 116(3): 291-303.
The information given here is for educational purposes only. References to commercial products, trade names, or suppliers are made with the understanding that no endorsement is implied and that no discrimination against other products or suppliers is intended.
Publication 3863 (POD-02-23)
By Curtis L. VanderSchaaf, PhD, Assistant Professor, Central Mississippi Research and Extension Center, Mississippi State University; Wayne Withers, Instructor, Logging Equipment Operator Academy, Hinds Community College; and David Livingston, Executive Director, Mississippi Loggers Association. The authors thank Rien Visser, PhD, Professor, University of Canterbury, and Han-Sup Han, PhD, Professor of Forest Operations, Northern Arizona University, for providing useful comments.
The Mississippi State University Extension Service is working to ensure all web content is accessible to all users. If you need assistance accessing any of our content, please email the webteam or call 662-325-2262.