From Contractor to Poultry Farmer
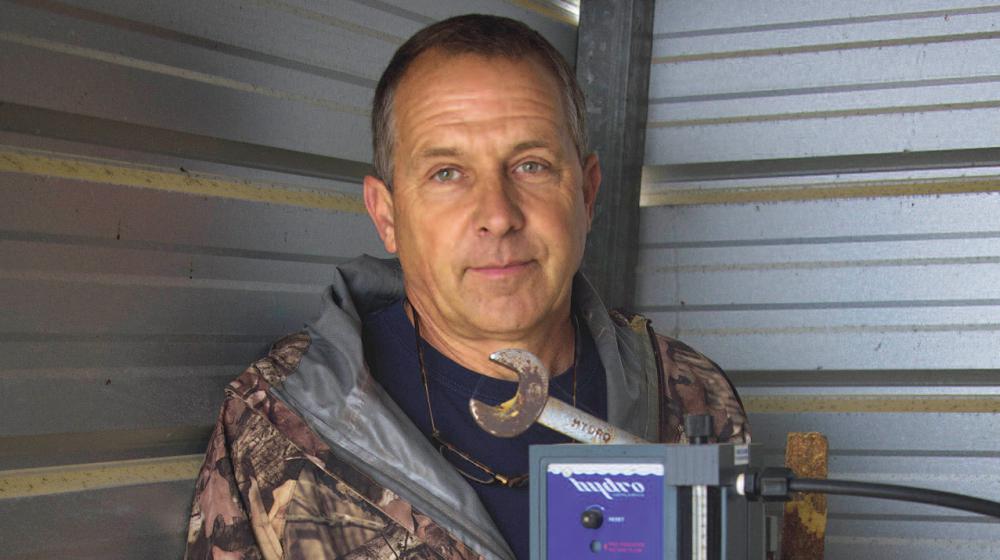
Joe Ellis, poultry producer
Extension helps Okolona producer improve profitability and maintain healthy birds
Joe Ellis knew almost nothing about chickens when he began raising them for Peco Foods, Inc., in 2008.
For the previous 20 years, he had been a construction contractor, and, although his father-in-law had chicken houses, Ellis had not been involved with that business. He learned to manage his six broiler houses and more than 140,000 chickens by reading, consulting with other growers, and watching his own chickens.
“I’d been in and out of my father-in-law’s chicken houses some, but I didn’t know anything about chickens,” explains Ellis, of Okolona. “I had a really good placement man with Peco. He helped me a lot. I also spent a lot of time sitting on a five-gallon bucket just watching my chickens.”
But in 2013, Ellis came across a problem he could not solve. The evaporative cooling pads that helped keep the chickens cool in high summer temperatures were dissolving. Growers add well or community water to the cooling pads located at one end of a house and run large exhaust fans located at the other end to help regulate the critical balance between temperature and humidity in the houses.
“I knew it had to be the water quality, but I couldn’t figure out how to adjust it,” Ellis says of the disintegrating cooling pads. “The pads were just melting, going away. They are supposed to last seven to ten years, and I’d only had them for three or four years.”
Replacing the pads more often was not financially feasible because they cost between $30,000 and $40,000. Ellis needed to find a fix.
So he decided to call the Mississippi State University Extension Service.
Tom Tabler, poultry specialist with Extension, took water samples to the MSU chemical lab. Scientists determined high levels of sodium and chloride in the untreated water, coupled with a high pH, were eroding the pads. Tabler helped him adjust the water quality by adding a gas chlorinator and a chemical pump that injects apple cider vinegar into the water.
That call to Extension became the first of many. Ellis has since developed a strong relationship with the educational organization and says it has helped him improve profitability and maintain healthy birds.
“After we got the water problem solved, Joe asked me about LED lighting,” Tabler says. “So I explained that LEDs do not affect the birds and that flock performance will be equal to incandescent bulbs, but LEDs do help reduce energy bills a good bit. LED bulbs use about 80 percent less energy than incandescent bulbs.”
That move has saved Ellis about $1,000 per month in energy costs, he says. Tabler also tested the chicken litter from Ellis’s barns as part of a statewide research project to get up-to-date nutrient values to help crop and livestock producers who use the litter for fertilizer.
“The Extension Service has been really good to me,” Ellis says. “Dr. Tabler has helped me tremendously. I’ve been well pleased with his recommendations.”
In fact, the Extension Service is now at the top of Ellis’s reference list. He talks often with Tabler over the phone and checks in regularly with the county Extension agent.
“Sometimes I call Dr. Tabler to find out what I can expect if there are changes I’m making,” Ellis explains. “I’ll call him if my chickens don’t look just right, and he can tell me what to do. I also see the county agent a lot about litter recommendations and if there are things I need to know relative to my county.
“I am indebted to Dr. Tabler and Extension.” Ellis’s conscientious approach contributes to his success, Tabler says.
“Joe is very meticulous,” Tabler says. “He is a very good farmer, and he wants to do what is right. He has a lot of faith in my ability. I’m grateful for that, and I try to be worthy of that faith. He pays attention and will take my advice or listen to other growers who can help him."